In the world of architectural concrete fabrication, innovation is key to achieving precise and visually stunning designs. At Concrete Works East, we harness the power of 3D fabrication to push the boundaries of creativity and functionality. By leveraging advanced techniques like CNC milling, 3D modeling for concrete, and mold building, we bring even the most intricate design concepts to life with unmatched accuracy.
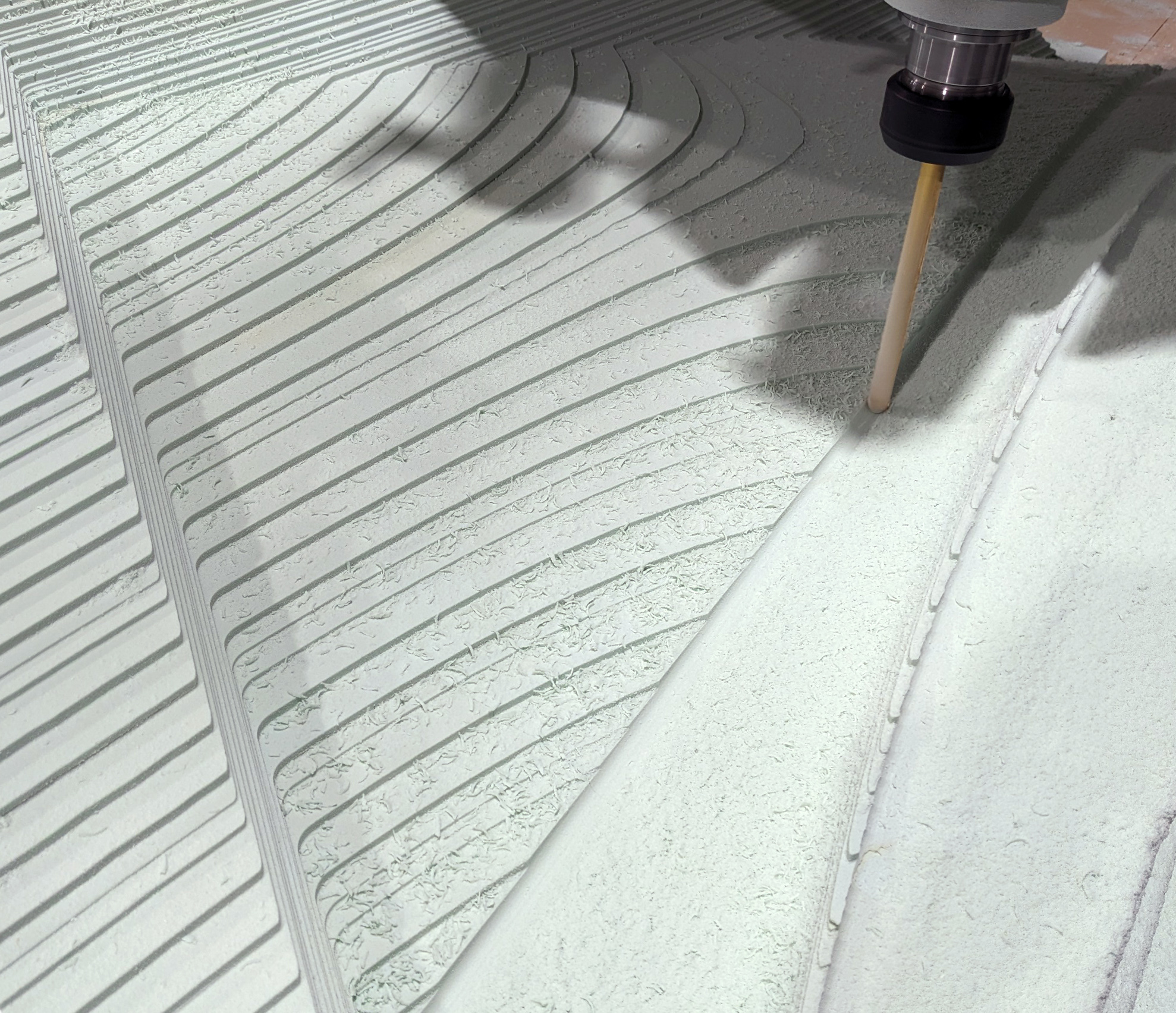
Custom 3D Concrete
Concrete has been a reliable, durable, sturdy building material for hundreds of years. This versatile material is moldable, which means it can take almost any shape. Advances in technology have made it possible for us to use modeling software and computer-controlled machines to design and create complex shapes. With this technology, we can fabricate almost any design, giving you the durability you need with the artistry you want.
At Concreteworks East, our mission is to bring any designer’s creative vision to life with concrete. As the popularity of these 3-dimensional complex and organic shapes continues to grow, we continue to invest in our in house fabrication capabilities to succeed on that mission. Paired with the use of glass fiber reinforced concrete, not only can we offer a concrete mix with superior durability, strength, and color development, we can now create concrete shapes that weren’t viable in years past.
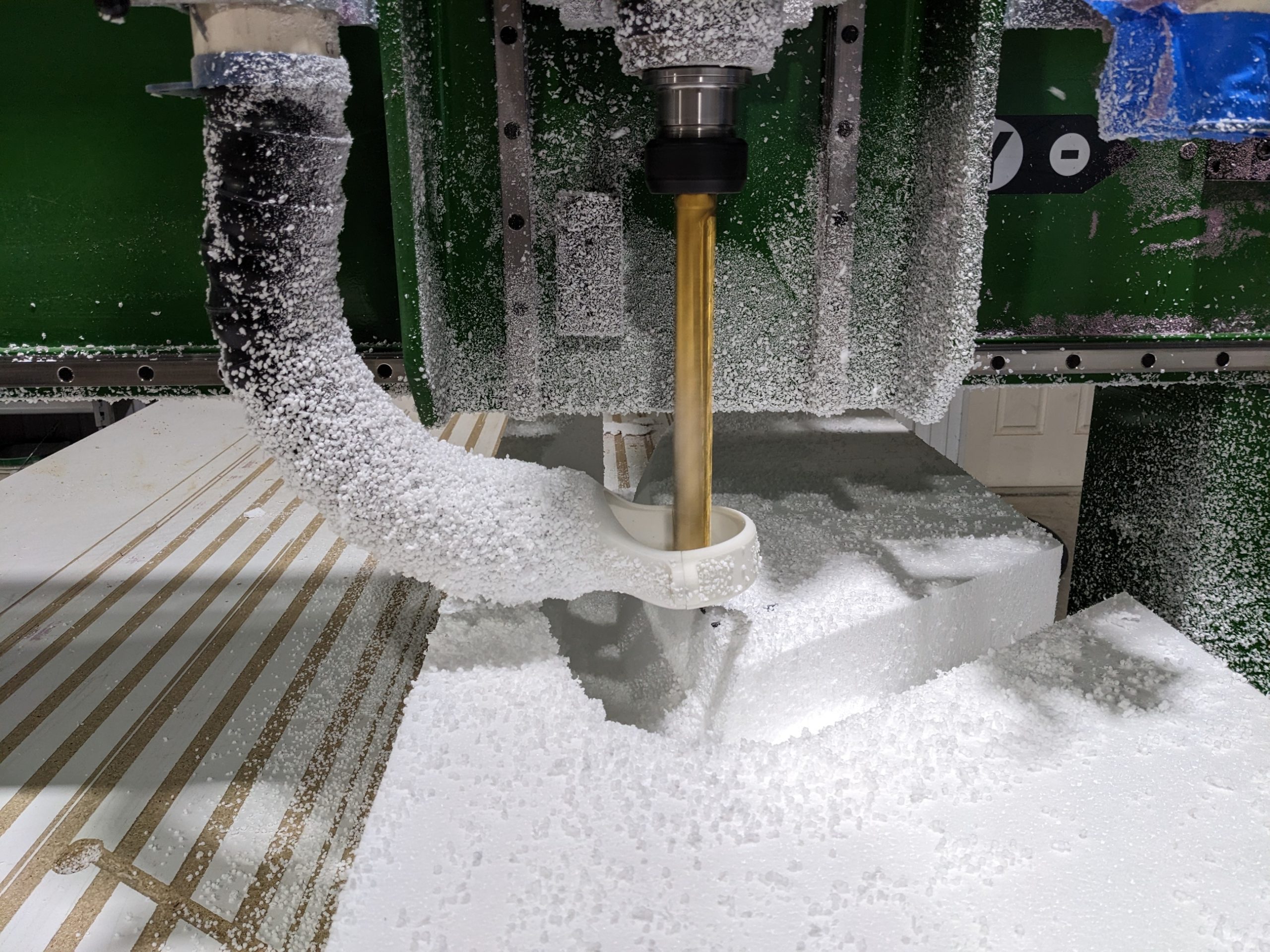
CNC Milling
CNC milling is the backbone of precision in 3D fabrication. This computer-controlled process allows us to create molds and templates with extraordinary accuracy, ensuring every detail is captured perfectly. By eliminating manual errors, CNC milling speeds up production and delivers consistent results, even for the most complex designs. From smooth surfaces to intricate patterns, CNC milling ensures that no detail is too small or too challenging.
Our Process
Get a behind-the-scenes look at the process behind our innovative and durable custom GFRC products. This three-part series gives an insightful overview of mold design & creation, milling, casting, fabrication, finishing, and crating.
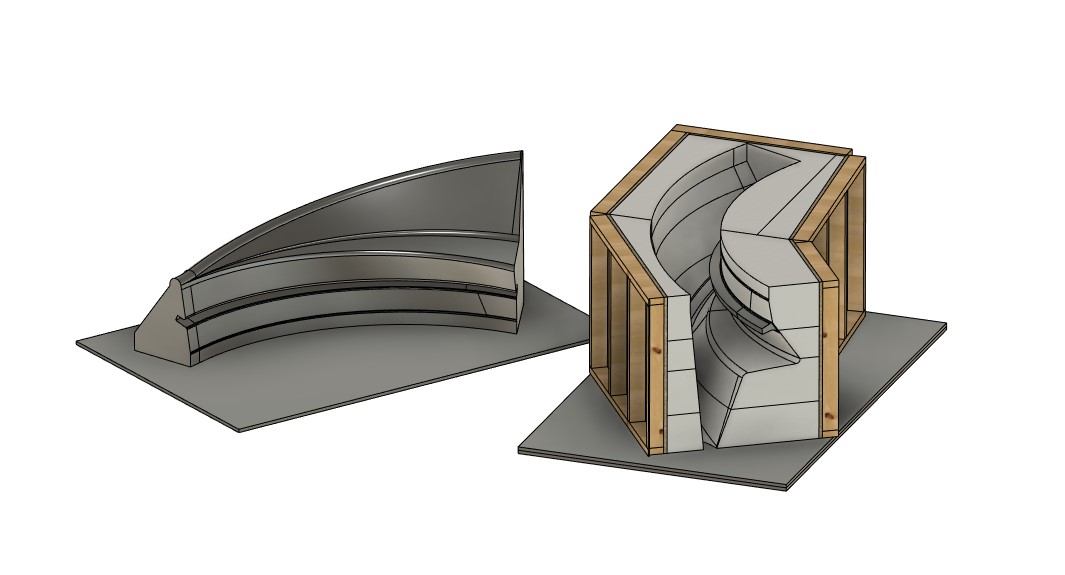
3D Modeling
Using cutting-edge 3D modeling for concrete, we bridge the gap between design concepts and physical reality. This software enables architects, designers, and clients to visualize their ideas in stunning detail before production begins. Clear and realistic renderings not only improve communication but also streamline the collaboration process, ensuring every stakeholder is aligned on the final design.
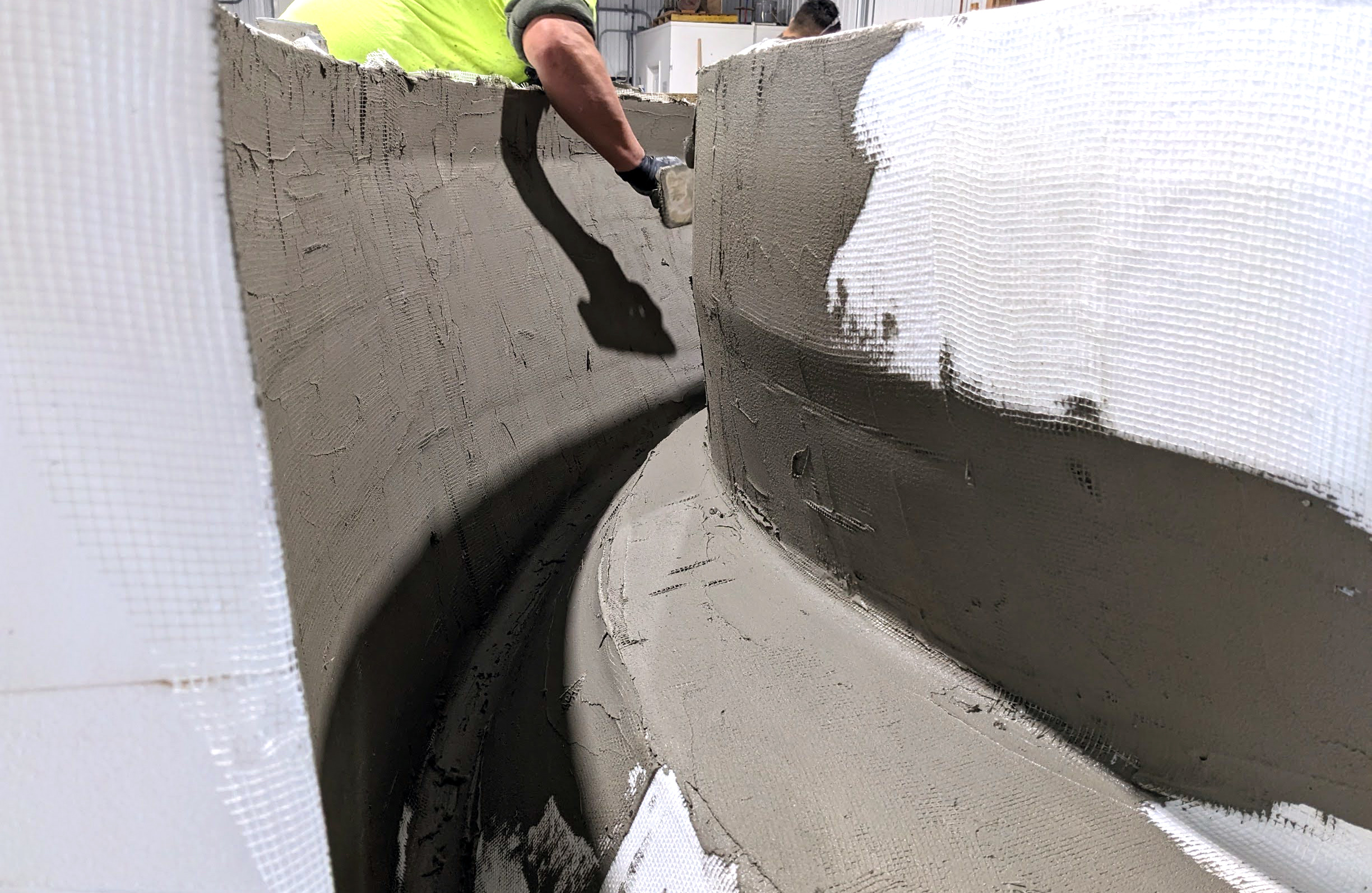
Mold Building
The final step in the 3D fabrication process is mold building. High-quality molds are crafted based on 3D models and CNC milling outputs, ensuring that the final concrete elements are both durable and precise. These molds are critical for achieving consistent results, especially for projects that require repeated casting. By prioritizing quality in mold construction, we ensure the longevity and reliability of every product.
Pairing 3D Fabrication with GFRC for Custom Concrete
One of the most exciting aspects of our 3D fabrication process is its seamless pairing with GFRC custom concrete. Glass Fiber Reinforced Concrete (GFRC) is a lightweight yet highly durable material that enhances the possibilities of custom concrete design. By combining GFRC’s strength and flexibility with our advanced fabrication techniques, we create architectural elements that are both beautiful and functional.
Applications of GFRC and 3D Fabrication:
- Custom Panels and Facades: Achieve intricate details and lightweight construction for building exteriors.
- Bespoke Concrete Furniture: Create unique, sculptural pieces that blend art and practicality.
- Architectural Features: Design one-of-a-kind staircases, decorative elements, and more.
Benefits of 3D Fabrication in Architectural Concrete
Precision and Accuracy
Advanced 3D fabrication techniques eliminate errors, ensuring that every element is made to exact specifications. This level of precision is essential for high-end architectural projects.
Customization
From complex geometric shapes to organic designs, 3D fabrication allows for unparalleled customization. Whether it’s a one-of-a-kind sculpture or a series of matching panels, the possibilities are endless.
Efficiency
Compared to traditional methods, 3D fabrication significantly reduces production timelines. This efficiency allows projects to move forward quickly without compromising on quality or design integrity.
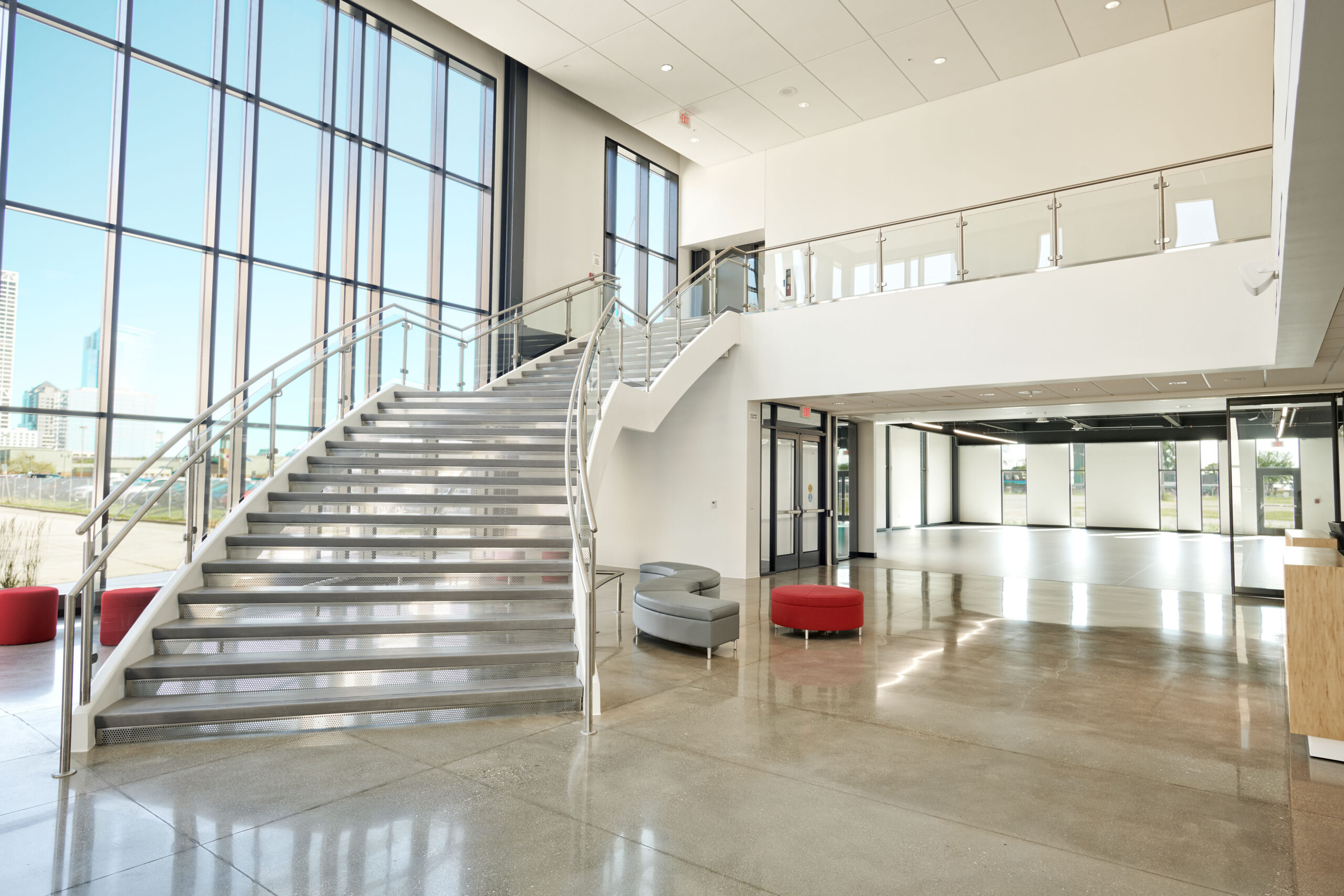
Showcase of Applications
Concrete Works East has used 3D fabrication to create stunning pieces for a variety of projects. Examples include:
- Architectural Panels and Facades: Elevate the exterior of any building with intricate, lightweight designs.
- Custom Furniture: Transform interiors with bespoke concrete tables, chairs, and decorative pieces.
- Artistic Staircases and Features: Add a bold statement to commercial or residential spaces with unique architectural elements.
Still curious?
Ready to explore the endless possibilities of 3D fabrication? Let Concrete Works East bring your vision to life with innovative techniques like CNC milling, 3D modeling for concrete, and mold building. Contact us today to discuss your project and discover how we pair these technologies with GFRC custom concrete to create exceptional architectural designs.
Check out more footage of our process!